PLAYING WITH FIRE 4
- David
- Feb 13, 2020
- 3 min read
Updated: Jan 21, 2022
BRONZE CASTING PROCESS: Post 4
MOLD MAKING
Often when I have described the bronze casting process some confusion creeps in at this point. I have a knack for creating confusion. The lost wax technique, which is what we are talking about here, usually involves two kinds of molds for any one figure. One mold is for making wax reproductions of the original form, and one mold is for pouring the bronze into. The first mold, the one made to reproduce the wax, is made of silicone rubber and plaster of Paris, and is reusable many times over. The second type of mold, the pouring mold, is always destroyed by the metal being poured into it, and thus must be remade every time a casting is to be made. We will come back to this refractory mold later.

If the original form is small and simple enough, and made of wax, and if it is intended to be a one-of-a-kind item, then a wax mold is not needed. But if the form is intended to be reproduced, or if the maker of the piece wants to insure that the original effort of sculpting is not lost to a casting failure, then it involves a mold for reproduction of that original form. The purpose of this wax mold is twofold: first, it allows for the reproduction of the form; secondly, it allows the artist to make larger figures hollow. Large bronzes are almost always hollow. When you do see large solid castings they are usually sand castings, due to the inherently collapsible nature of sand as the metal shrinks and more often than not, these castings are of a utilitarian nature as opposed to art castings. Solid castings, besides being terribly expensive and exceedingly heavy, are quite vulnerable to shrink defects (porosity) as they cool, and are generally impractical for finely worked surfaces. A hollow bronze figure is heavy enough without it being more than about a quarter inch thick.
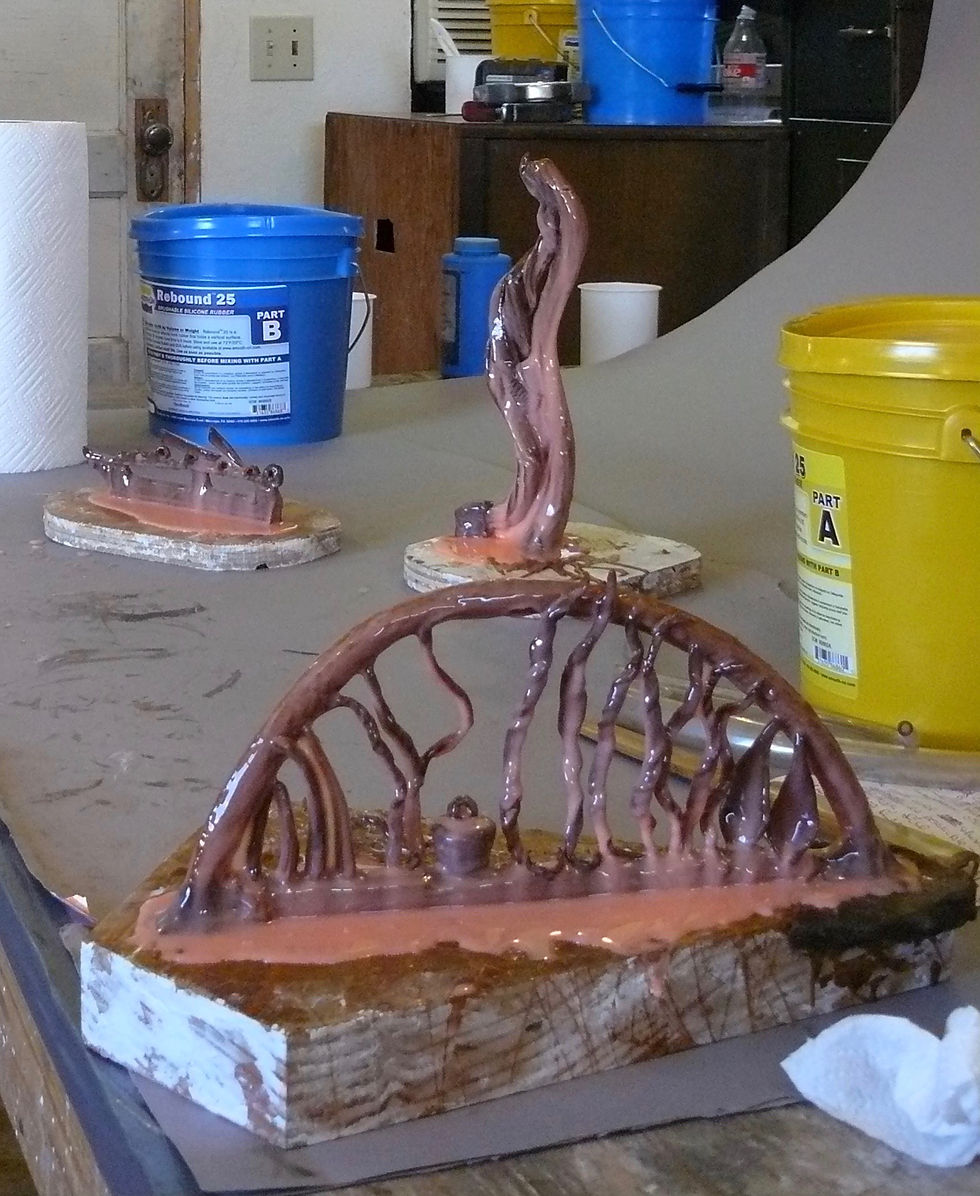
The wax mold is created by painting silicone rubber over the original figure. The rubber is very faithful to the textures, allowing for great detail to be preserved as intended. A thickness of perhaps 1/4th inch of rubber is built up over several coats until it can hold its shape fairly well. After the rubber is cured, a backing mold, or “mother mold” is made of plaster-of-Paris, to make certain that the rubber mold is held in exactly the correct orientation. The mother mold is usually made of two separate shells, like a clam shell, that can be pulled free of the rubber mold inside. Something very simple like a stylized fish can be reproduced by a single mold, but most sculptures will be cut into several, or many manageable-sized and shaped pieces. Each piece will be reproduced by its own mold. My pieces sometimes have thirty or more molds.
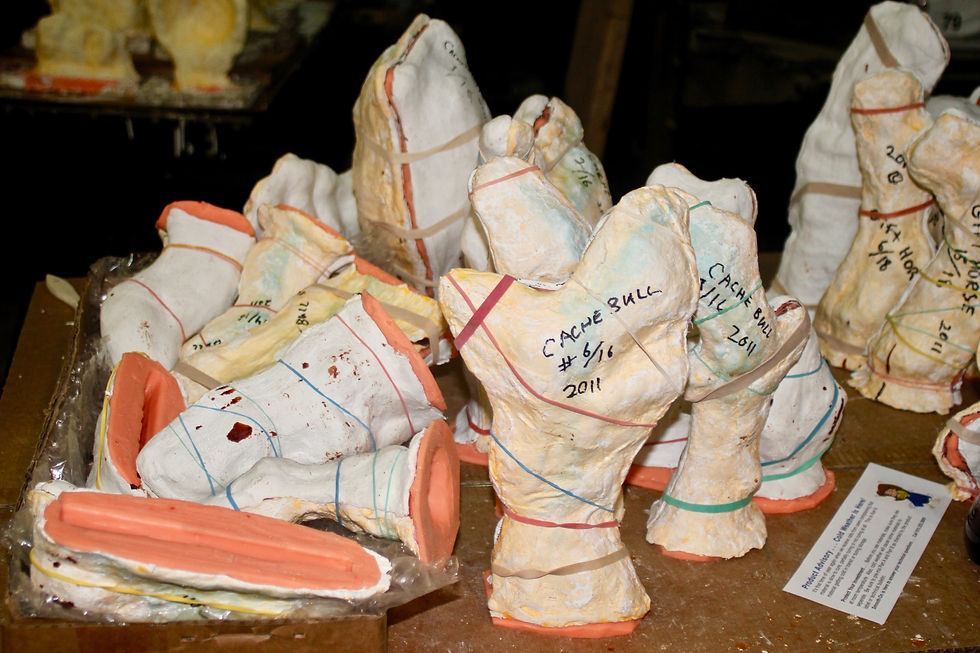

When the plaster is cured and dry, the mother mold is parted on the predetermined parting lines, and the rubber is cut through to the original form on these same lines. This line will show in the waxes after they are poured, and appears as a seam. In the perfectly registered (positioned) mold, this seam is all but invisible, but can usually be found with a bit of looking.
Once you have a mold of a piece, it becomes possible to reproduce the form many times over. This is why bronze sculptures are almost always done in editions. The expense of the mold making usually wipes out any income one might be hoping for on a single casting. So multiple editions become the norm. How many pieces might be cast in an edition is a matter of choice. A sculptor might choose to do a thousand castings, or they may choose to do three.
Part of the value of a bronze sculpture is in its rarity. Part of its value is in the fame or marketability of the piece, or the artist. There is no one way artists decide how many of something they will make. I make nine castings of most pieces. Most artists make larger editions. But because I do the foundry work myself, nine is about all I want to do. I like that whoever buys one of my pieces is getting the real deal, something that I made from start to finish, but it limits my edition size.
Comments